-
- ИССЛЕДОВАТЬ
-
-
-
-
-
-
-
Steel Wire Rope: Strength, Flexibility, and Industrial Power
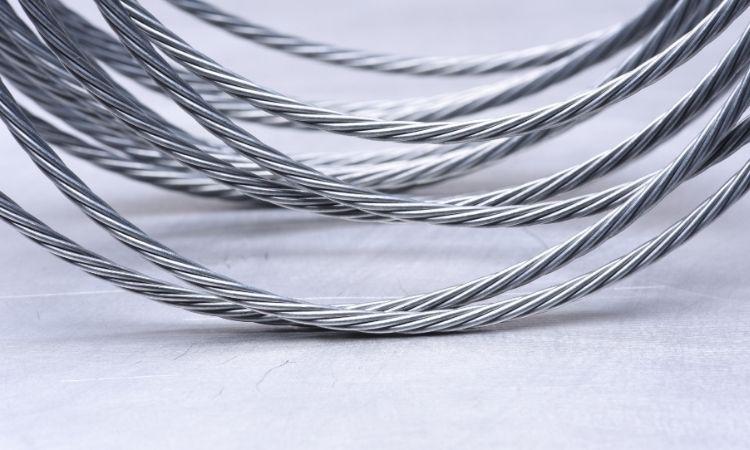
Steel wire rope is not just a tool—it’s a symbol of strength, endurance, and precision. Found at the core of industries ranging from construction and mining to shipping and aviation, this twisted marvel is engineered to perform under extreme pressure. Designed with strands of high-tensile steel wound into helical formations, steel wire ropes combine flexibility with incredible load-bearing capacity. Whether it's hoisting massive cargo, anchoring suspension bridges, or operating cranes on high-rise structures, steel wire ropes carry out tasks where failure is not an option.
Behind their rugged appearance lies a meticulous design. The number of strands, the type of core, the direction of lay—all these factors are tailored based on specific applications. Some ropes prioritize flexibility for dynamic movement, while others focus on resistance to abrasion, crushing, or fatigue. This makes the steel wire rope not just a product, but a highly customizable solution to mechanical challenges.
Expert Market Research Insight on Steel Wire Rope Applications
According to Expert Market Research, the demand for steel wire ropes is directly tied to their reliability and performance in high-stakes environments. Their widespread usage across heavy-duty sectors like marine, oil and gas, infrastructure, and lifting machinery makes them an integral part of the industrial supply chain. Expert Market Research notes that customization, technological upgrades in rope manufacturing, and material quality are key drivers of operational excellence. As industries continue to modernize, steel wire ropes remain relevant by evolving in strength, corrosion resistance, and fatigue life—offering a perfect balance between tradition and innovation in industrial engineering.
The Engineering Behind the Rope: What Makes Steel Wire Rope So Unique?
Steel wire ropes are composed of multiple wires twisted together to form strands, which are then helically laid around a core. This structure allows for flexibility while maintaining extreme tensile strength. The rope's design determines its resistance to rotation, crushing, kinking, or stretching, making each variant ideal for a particular task.
The core may be made of fiber for flexibility or steel for added strength and resistance to deformation. The outer strands come in different constructions such as 6x19, 6x36, or 8x19, indicating the number of wires and their thickness. A finer wire count generally offers greater flexibility, whereas thicker wires offer better abrasion resistance. This intricate architecture is what makes the steel wire rope dependable in environments where even the smallest error can lead to catastrophic failure.
Applications That Rely on the Unseen Force of Steel Wire Rope
You might not see it often, but steel wire rope is all around you—quietly supporting some of the most critical operations in the world. In the construction industry, it's the lifeline of cranes, elevators, and scaffolding systems. In maritime settings, it helps anchor ships and manage cargo on dockyards. In mining, it’s responsible for lifting tons of material from deep below the surface with mechanical precision.
Aviation and aerospace sectors use it in control cables, while theaters use miniature versions for hoisting stage sets. Even the scenic cable cars and suspension bridges we admire rely on this powerhouse. Each application brings its own set of stressors—moisture, load variation, friction—and the rope is specifically chosen to endure them all. It's not just about lifting weight; it's about doing so consistently, safely, and over thousands of cycles.
Maintenance, Safety, and Best Practices: Extending Lifespan and Reliability
Even the strongest wire rope needs proper handling and regular maintenance. Inspection routines are essential for identifying fraying wires, corrosion, and fatigue. Regular lubrication ensures that internal wires do not rub dry against each other, reducing wear and tear. Replacing a worn-out rope before it fails is not just good practice—it’s essential for workplace safety.
Handling also matters. Steel wire ropes should be stored in dry, covered spaces and wound or unwound using spooling techniques to avoid kinks. Proper tension, alignment, and installation extend their life and maintain performance integrity. Remember, a steel wire rope is only as strong as its weakest strand—so every detail matters.
Future-Forward Innovations: Smart Coatings and Stronger Alloys
The evolution of steel wire rope is far from over. Advanced coatings such as zinc-aluminum and polymer sheaths are being used to enhance corrosion resistance in marine and coastal environments. Stainless steel variants and compacted ropes are growing in popularity for their sleek design and higher load capacities.
Emerging technologies like embedded sensors for load monitoring, real-time tension analysis, and condition alerts are pushing the boundaries of what these ropes can do. These smart solutions are especially critical in high-risk industries, where real-time data can prevent failures and enhance operational safety.
Silent Strength You Can Count On
Steel wire ropes may not grab headlines, but they play an essential role in the world’s infrastructure, movement, and mechanics. From supporting the tallest buildings to diving into the deepest mines, they offer silent strength, enduring reliability, and unmatched engineering brilliance.
With continuous innovation and adherence to safety and performance standards, steel wire ropes continue to adapt to the growing needs of the modern world. They aren’t just tools—they’re lifelines. Whether you're building bridges or operating cranes, you can trust the integrity of steel wire rope to get the job done, again and again.
- Art
- Causes
- Crafts
- Dance
- Drinks
- Film
- Fitness
- Food
- Игры
- Gardening
- Health
- Главная
- Literature
- Music
- Networking
- Другое
- Party
- Religion
- Shopping
- Sports
- Theater
- Wellness