Nylon Fabric Manufacturing Plant Project Report 2025: Project Report and Setup Guide
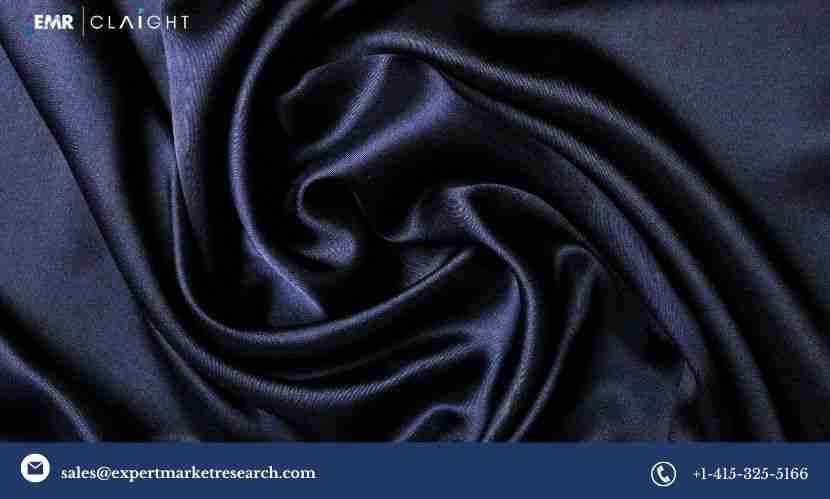
Introduction
Nylon fabric is one of the most widely used synthetic fibers in the textile industry, owing to its excellent durability, elasticity, and versatility. As a material, nylon is used in a variety of applications, ranging from clothing and sportswear to industrial products, automotive components, and more. The growing demand for high-performance textiles has driven the global nylon fabric market, and this trend is expected to continue as the textile industry evolves. This Nylon Fabric Manufacturing Plant Project Report aims to provide an in-depth analysis of setting up a nylon fabric manufacturing plant. It covers market trends, manufacturing processes, raw materials, plant requirements, regulatory considerations, and financial projections, providing valuable insights for investors and entrepreneurs interested in establishing a nylon fabric manufacturing facility. By understanding the key factors involved in the production of nylon fabric, this report will help ensure the successful establishment and operation of a manufacturing plant.
Market Overview
Global Market for Nylon Fabric
The nylon fabric market has shown consistent growth due to its broad range of applications and favorable properties. Nylon is used in everything from apparel to industrial applications, contributing significantly to its demand. The increasing preference for high-performance fabrics, along with technological innovations in the textile industry, has expanded the potential for nylon fabric manufacturing.
Key factors influencing the growth of the nylon fabric market include:
-
Versatility in Applications: Nylon fabrics are used in various applications, including clothing, upholstery, automotive, packaging, and sports equipment. Their wide range of uses increases demand across different industries.
-
Durability and Strength: Nylon is known for its strength and resistance to wear and tear. This makes it an ideal choice for products like activewear, outdoor clothing, and industrial fabrics that require long-lasting durability.
-
Technological Advancements: Innovations in fabric treatments and finishes are enabling nylon fabrics to be more versatile and functional. For example, advances in moisture-wicking and UV-protection technologies have made nylon fabrics more appealing to consumers.
-
Growing Apparel and Fashion Industry: The increasing demand for functional, high-performance, and stylish clothing has led to higher consumption of nylon fabrics in the fashion and activewear sectors.
-
Environmental Concerns: As sustainability becomes a major focus within the textile industry, manufacturers are exploring eco-friendly alternatives and techniques for producing nylon fabrics. This includes using recycled nylon and minimizing waste during production.
Get a Free Sample Report with Table of Contents@
Regional Insights
-
North America: The U.S. and Canada are significant markets for nylon fabric, particularly in the automotive, clothing, and industrial sectors. The demand for high-quality, durable fabrics in these regions is driving market growth.
-
Europe: The European market for nylon fabric is driven by a strong fashion industry, automotive manufacturing, and a growing focus on sustainable textiles. The increasing interest in eco-friendly nylon alternatives has also played a role in market growth.
-
Asia-Pacific: The Asia-Pacific region, particularly countries like China, India, and Japan, holds the largest market share due to the rapid expansion of the textile and garment industries. Low labor costs and the presence of key manufacturers make this region a hub for nylon fabric production.
-
Latin America and Middle East: Emerging markets in Latin America and the Middle East are gradually increasing their demand for nylon fabric, particularly for use in the automotive, sportswear, and consumer goods industries.
Feasibility Study for Nylon Fabric Manufacturing Plant
Site Selection
Choosing the right location for the nylon fabric manufacturing plant is crucial for the success of the business. The following factors should be considered:
-
Proximity to Raw Materials: Nylon fabric manufacturing relies on key raw materials such as caprolactam, hexamethylenediamine, and adipic acid. The plant should be located near suppliers of these chemicals to ensure cost-effective and timely procurement.
-
Labor Availability: A skilled workforce is essential for operating the plant efficiently. The location should be close to urban areas or industrial hubs with an adequate supply of skilled labor, including textile engineers, machine operators, and quality control staff.
-
Logistics and Distribution: The location of the plant should provide easy access to transportation infrastructure, including highways, railways, and ports, to facilitate the import of raw materials and the distribution of finished products.
-
Regulatory Compliance: The site should be in an area that adheres to environmental and industrial regulations. The plant should have access to necessary utilities and infrastructure to ensure smooth operations.
Regulatory Compliance
Nylon fabric manufacturing plants must comply with various local and international regulations, particularly in the areas of environmental impact, worker safety, and product quality. Key regulatory aspects include:
-
Environmental Regulations: The production of nylon fabric can lead to emissions, chemical waste, and water usage. Compliance with environmental regulations regarding waste disposal, air quality, and water treatment is essential to minimize the plant’s ecological footprint.
-
Occupational Health and Safety: The plant must adhere to safety standards to ensure the health and safety of workers. This includes providing proper protective gear, training on machine operation, and adhering to industrial safety guidelines.
-
Quality Control Standards: The plant must adhere to international quality control standards such as ISO 9001 to ensure consistent production and product quality. This includes inspecting raw materials, monitoring production processes, and conducting final product testing.
-
Sustainability Regulations: With the growing emphasis on sustainability, the plant should explore options for using recycled materials, minimizing waste, and adopting energy-efficient practices. Meeting sustainability standards may also provide marketing advantages in eco-conscious markets.
Raw Materials and Procurement
The main raw materials required for nylon fabric production are:
-
Caprolactam: Caprolactam is a key raw material used in the production of nylon 6, one of the most common types of nylon fabric. It is derived from petrochemicals and is polymerized to create nylon fibers.
-
Hexamethylenediamine (HMD): Hexamethylenediamine is another important raw material used in the production of nylon 6,6, a variant of nylon commonly used in textiles and industrial applications.
-
Adipic Acid: Adipic acid is a key ingredient used in the production of nylon 6,6 fibers, which are known for their strength and durability.
-
Dye and Finishing Chemicals: Various dyes and chemicals are used to color and finish nylon fabrics, making them suitable for different applications in the fashion, automotive, and industrial sectors.
Establishing strong relationships with reliable suppliers of these raw materials will ensure a consistent supply chain and help keep costs manageable.
Manufacturing Process
The manufacturing process of nylon fabric involves several key stages, including:
-
Polymerization: Nylon is produced through a polymerization process where raw materials such as caprolactam, hexamethylenediamine, and adipic acid undergo chemical reactions to form nylon polymers.
-
Spinning: The nylon polymer is then melted and extruded into filaments through a process known as spinning. These filaments are then cooled and solidified.
-
Weaving or Knitting: The nylon filaments are woven or knitted into fabric using looms or knitting machines. The type of fabric produced will depend on the weaving or knitting pattern used.
-
Dyeing and Finishing: Once the fabric is woven or knitted, it is dyed using various chemicals to achieve the desired color. Finishing processes such as heat-setting, water repellency, and anti-static treatments may also be applied to enhance the fabric's properties.
-
Quality Control: Throughout the manufacturing process, quality control checks are conducted to ensure the nylon fabric meets the required standards. This includes checking for defects, strength, color consistency, and texture.
-
Packaging: Once the fabric passes quality control, it is packaged and prepared for shipment to customers, including garment manufacturers, upholstery suppliers, and other industries that require nylon fabrics.
Workforce Requirements
The nylon fabric manufacturing plant will need a skilled workforce to handle the various aspects of production, including:
-
Production Managers: Oversee the day-to-day operations of the manufacturing process to ensure efficiency and adherence to quality standards.
-
Textile Engineers: Design and optimize the production processes for the nylon fabric to ensure high-quality output and cost-efficiency.
-
Machine Operators: Operate the machinery used for spinning, weaving, and dyeing the nylon fabric.
-
Quality Control Inspectors: Ensure that the final product meets quality standards, including strength, durability, color consistency, and finish.
-
Maintenance Staff: Maintain the machinery and equipment to prevent downtime and ensure smooth operations.
Financial Considerations
Setting up a nylon fabric manufacturing plant requires significant capital investment and ongoing operational costs. Key financial factors to consider include:
-
Initial Investment: The initial investment will include costs related to land acquisition, building construction, machinery, equipment, and raw material procurement. The cost of meeting regulatory requirements should also be factored in.
-
Operational Costs: Ongoing costs will include wages, raw materials, utilities (such as electricity and water), maintenance, and logistics.
-
Revenue Projections: Revenue will depend on the plant’s production capacity, product pricing, and market demand. The growth of industries such as fashion, automotive, and furniture manufacturing will provide opportunities for sales.
-
Break-even Analysis: A break-even analysis helps estimate when the plant will cover its initial investment and start generating profits.
-
Profitability and Return on Investment (ROI): Estimating ROI is essential for evaluating the long-term financial viability of the plant. Financial projections should consider the plant’s growth potential, market trends, and competitive landscape.
Marketing and Distribution Strategy
To effectively market and distribute the nylon fabric, manufacturers should consider the following:
-
Branding and Promotion: Building a strong brand identity will help differentiate the product in a competitive market. Highlighting the durability, versatility, and eco-friendly aspects of the fabric can appeal to specific market segments.
-
Retail Partnerships: Collaborating with textile distributors, garment manufacturers, and upholstery suppliers will help expand the product’s reach.
-
Export Opportunities: Expanding into international markets, particularly in Asia-Pacific and North America, can provide growth opportunities.
-
Customer Support: Offering excellent customer service, including fast delivery times and responsive communication, will help build long-term relationships with clients.
Explore More Report
https://www.expertmarketresearch.com/articles/top-coffee-companies
Media Contact
Company Name: Claight Corporation
Contact Person: Peter Fernandas, Corporate Sales Specialist — U.S.A.
Email: [email protected]
Toll Free Number: +1–415–325–5166 | +44–702–402–5790
Address: 30 North Gould Street, Sheridan, WY 82801, USA
Website: www.expertmarketresearch.com
Aus Site: https://www.expertmarketresearch.com.au
- Art
- Causes
- Crafts
- Dance
- Drinks
- Film
- Fitness
- Food
- Oyunlar
- Gardening
- Health
- Home
- Literature
- Music
- Networking
- Other
- Party
- Religion
- Shopping
- Sports
- Theater
- Wellness